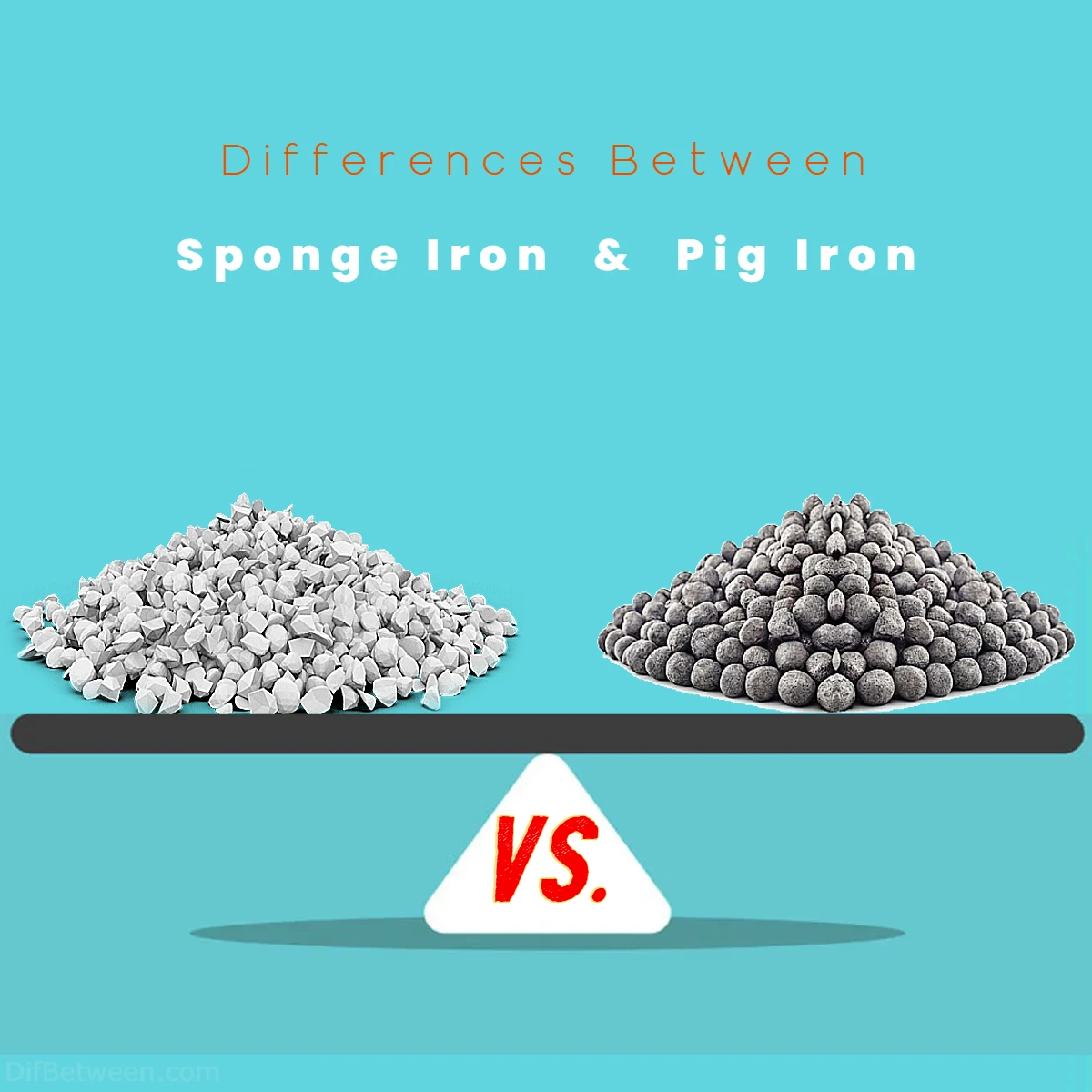
Aspect | Sponge Iron | Pig Iron |
---|---|---|
Production Process | Direct reduction process | Blast furnace smelting process |
Chemical Composition | Low carbon, minimal impurities | High carbon, variable impurities |
Physical Properties | Porous, less dense, softer | Dense, harder, brittle |
Applications | Steel production, casting, more | Cast iron, foundry work, alloy production, some steelmaking |
Environmental Impact | Lower carbon emissions, energy-efficient, less waste | Higher carbon emissions, energy-intensive, more waste |
Cost Considerations | Capital-intensive, lower operational costs | Capital-efficient, higher operational costs |
Technological Advancements | Ongoing advancements in direct reduction technology | Ongoing advancements in blast furnace technology |
Future Sustainability Goals | Suitable for organizations aiming to reduce carbon footprint | Appropriate for organizations prioritizing other aspects like cost savings |
Recyclability | Can be used in recycling processes due to low impurity content | Used primarily as a primary raw material rather than recycled |
Raw Material Costs | Cost influenced by iron ore and reductants | Cost influenced by iron ore, coke, and limestone |
Hardness | Relatively soft and malleable | Notably harder and more brittle |
Sponge iron, with its porous, spongy allure, stands in stark contrast to the dense, robust persona of pig iron. These distinctions extend beyond mere appearance, encompassing production processes, chemical compositions, environmental impact, and application suitability.
Differences Between Sponge Iron and Pig Iron
The primary differences between Sponge Iron and Pig Iron lie in their production processes and chemical compositions. Sponge Iron is produced through direct reduction, resulting in a low-carbon, pure iron with minimal impurities, making it ideal for applications like steel production. On the other hand, Pig Iron is derived from blast furnace smelting, boasting a higher carbon content and variable impurities, making it suitable for cast iron production and foundry work. These distinctions in production methods and chemical compositions shape their respective applications and environmental impacts, offering distinct choices for various industrial needs.
1. Introduction to Iron Types
Before we dive into the distinctions, let’s establish a basic understanding of what sponge iron and pig iron actually are.
Sponge Iron
Sponge iron, also known as direct-reduced iron (DRI), is a type of iron produced by reducing iron ore (typically in the form of pellets or lumps) using a reducing gas or solid reductant, such as coal. This reduction process occurs at a lower temperature compared to traditional iron smelting, resulting in a porous, sponge-like structure, hence the name “sponge iron.”
Pig Iron
Pig iron, on the other hand, is an intermediate product in the iron production process. It is typically created by smelting iron ore (usually in the form of iron oxides) in a blast furnace. The resulting material is high in carbon content and contains impurities, making it brittle and unsuitable for most applications. Pig iron serves as a crucial raw material for the production of steel and cast iron.
Now that we have a basic understanding of these iron types, let’s explore their differences in more detail.
2. Production Process
One of the most significant differences between sponge iron and pig iron lies in their respective production processes.
Production of Sponge Iron
The production of sponge iron involves a process known as direct reduction, which is typically carried out in either a rotary kiln or a fluidized bed reactor. Here’s a step-by-step breakdown of the process:
- Iron Ore Preparation: Iron ore, often in the form of pellets or lumps, is prepared and heated to remove any moisture.
- Reduction: The prepared iron ore is introduced into the reduction reactor along with a reducing gas (commonly natural gas or coal). This gas reacts with the iron ore, reducing it to metallic iron. The reaction occurs at temperatures below the melting point of iron, preventing the ore from liquefying.
- Formation of Sponge Iron: As the reduction progresses, the iron ore transforms into a porous, sponge-like structure, retaining its metallic properties.
- Cooling and Compaction: The sponge iron is then cooled and compacted into briquettes or other suitable forms for storage and transportation.
Production of Pig Iron
In contrast, pig iron is produced through a different process, known as iron smelting, which primarily involves the use of a blast furnace. Here’s how pig iron is made:
- Iron Ore and Coke Preparation: Iron ore, along with coke (a high-carbon fuel derived from coal) and limestone, is charged into the blast furnace. The coke serves as both a fuel and a reducing agent.
- Combustion and Reduction: Air is blown into the furnace, causing the coke to combust and release heat. This heat, in turn, reduces the iron ore to molten iron, while impurities combine with the limestone to form slag.
- Separation: The molten iron and slag are separated due to their differing densities, with the iron sinking to the bottom of the furnace.
- Tapping and Casting: The molten pig iron is periodically tapped from the furnace and cast into molds, forming pig iron ingots or pigs.
As you can see, the fundamental distinction in production processes is that sponge iron is created through a direct reduction process, while pig iron is the result of iron smelting in a blast furnace.
3. Chemical Composition
The chemical composition of sponge iron and pig iron is another crucial aspect that sets them apart.
Chemical Composition of Sponge Iron
Sponge iron is characterized by its relatively high purity. During the direct reduction process, impurities are removed, resulting in an iron product with a low carbon content and minimal other alloying elements. The typical chemical composition of sponge iron includes:
- Iron (Fe): Over 90%
- Carbon (C): Usually less than 0.1%
- Silicon (Si): Minimal
- Phosphorus (P) and Sulfur (S): Low levels
This high purity makes sponge iron suitable for various applications where a clean, low-alloy iron is required.
Chemical Composition of Pig Iron
Pig iron, in contrast, has a significantly different chemical composition. It is characterized by its high carbon content and the presence of various impurities. The typical chemical composition of pig iron includes:
- Iron (Fe): Around 92-94%
- Carbon (C): Approximately 3-4%
- Silicon (Si): Varies but can be substantial
- Phosphorus (P) and Sulfur (S): Can be relatively high
The high carbon content and impurities in pig iron render it unsuitable for most engineering applications, but it serves as a crucial raw material for the production of steel and cast iron.
4. Physical Properties
The physical properties of sponge iron and pig iron reflect their respective production processes and chemical compositions.
Physical Properties of Sponge Iron
- Appearance: Sponge iron has a porous, sponge-like appearance with a metallic luster.
- Density: Sponge iron is less dense than pig iron due to its porous structure.
- Melting Point: The melting point of sponge iron is typically higher than that of pig iron due to its lower carbon content.
- Hardness: It is relatively soft and malleable.
Physical Properties of Pig Iron
- Appearance: Pig iron appears as dense, brittle, and hard metallic material.
- Density: Pig iron is denser compared to sponge iron due to its compact, non-porous structure.
- Melting Point: Pig iron has a lower melting point than sponge iron due to its higher carbon content.
- Hardness: It is notably harder and more brittle than sponge iron.
These physical properties have significant implications for their respective uses and applications.
5. Applications
The differences in chemical composition and physical properties of sponge iron and pig iron directly impact their applications.
Applications of Sponge Iron
Sponge iron finds use in various industries, including:
- Steel Production: Sponge iron is a crucial raw material for steelmaking through the electric arc furnace (EAF) or induction furnace route. Its low impurity content makes it suitable for producing high-quality steel.
- Iron Casting: Sponge iron can be used in certain casting applications, particularly when a low-carbon iron is required.
- Powder Metallurgy: It is used as a feedstock in powder metallurgy processes, where powdered metals are pressed and sintered to create various components.
- Welding Electrodes: Sponge iron can serve as a raw material in the production of welding electrodes.
Applications of Pig Iron
Pig iron, due to its unique properties, is primarily used in the following applications:
- Steel Production: Pig iron is a key ingredient in the production of steel through the basic oxygen furnace (BOF) or the open-hearth furnace (OHF) route. Its high carbon content acts as a carbon source during steelmaking.
- Cast Iron Production: Pig iron is the primary raw material for the production of cast iron, which is used in various industries for making pipes, engine blocks, and more.
- Foundry Applications: Foundries use pig iron to create intricate castings that require high carbon content.
- Alloy Production: Pig iron can be alloyed with other elements to produce various types of alloyed iron.
In summary, sponge iron is favored in applications where a cleaner, low-carbon iron is essential, while pig iron is primarily used as a raw material for further refining into steel and cast iron.
6. Environmental Considerations
The production of both sponge iron and pig iron has environmental implications, but they differ in their environmental impact.
Environmental Impact of Sponge Iron Production
Sponge iron production is generally considered to be more environmentally friendly compared to traditional pig iron production. Here’s why:
- Lower Carbon Emissions: The direct reduction process used to make sponge iron typically produces fewer carbon emissions than iron smelting in a blast furnace.
- Energy Efficiency: The direct reduction process is often more energy-efficient because it operates at lower temperatures.
- Reduced Waste: The process generates fewer byproducts and less slag waste compared to iron smelting.
However, it’s essential to note that the environmental impact can vary depending on the specific technologies and practices employed in sponge iron production.
Environmental Impact of Pig Iron Production
Pig iron production, especially through the blast furnace route, is associated with several environmental challenges:
- High Carbon Emissions: The use of coke in the blast furnace results in substantial carbon dioxide emissions, contributing to greenhouse gas emissions.
- Energy Intensive: The blast furnace process is energy-intensive, consuming significant amounts of fossil fuels.
- Waste Generation: Pig iron production generates large amounts of slag, which can be environmentally problematic if not properly managed.
Given the environmental concerns associated with pig iron production, there is a growing interest in cleaner and more sustainable iron production methods, including the use of alternative fuels and technologies.
7. Cost Considerations
Cost considerations are crucial in choosing between sponge iron and pig iron for specific applications.
Cost Considerations for Sponge Iron
- Production Costs: The production of sponge iron may involve higher capital costs for direct reduction plants and equipment. However, operational costs, including energy consumption, can be lower.
- Raw Material Costs: The cost of iron ore and reductants (such as natural gas or coal) significantly impacts the overall cost of sponge iron production.
Cost Considerations for Pig Iron
- Production Costs: Pig iron production in blast furnaces often involves lower capital investment but higher operational costs due to the energy-intensive nature of the process.
- Raw Material Costs: The cost of iron ore, coke, and limestone plays a significant role in determining the cost of pig iron production.
When choosing between sponge iron and pig iron, businesses and industries must carefully evaluate the overall cost structure and market conditions to make informed decisions.
8. Future Trends in Iron Production
As we look to the future, it’s essential to consider the evolving trends in iron production and how they might impact the use of sponge iron and pig iron.
Green Technologies
One of the most significant trends in the iron and steel industry is the adoption of green technologies. With growing environmental concerns and stricter emissions regulations, there is a push to reduce the carbon footprint of iron production. This trend benefits sponge iron, which generally has a lower carbon footprint compared to pig iron. As technologies like hydrogen-based reduction processes and carbon capture and utilization (CCU) continue to develop, they may further enhance the environmental credentials of sponge iron.
Recycling and Circular Economy
The concept of a circular economy is gaining traction across industries, including iron and steel. Recycling scrap steel and iron is seen as an environmentally friendly and economically viable option. In this context, sponge iron may find increased use as a raw material in recycling processes due to its low impurity content. However, pig iron will continue to play a role in the production of new steel, especially when using primary raw materials.
Alternative Iron Sources
Research into alternative iron sources is ongoing. This includes exploring unconventional sources of iron, such as iron sands and mining low-grade iron ores. These alternative sources may impact the availability and cost of raw materials for both sponge iron and pig iron production.
Energy Efficiency
Energy efficiency remains a key focus in iron production. Both sponge iron and pig iron processes are likely to see improvements in energy efficiency, impacting their operational costs and environmental performance. Innovations in energy recovery and utilization may play a crucial role in this aspect.
Sponge Iron vs Pig Iron: Which One is Right Choose?
Choosing between sponge iron and pig iron can be a crucial decision, especially if you’re involved in industries that rely on iron as a raw material. Each type of iron has its own set of characteristics and applications, and selecting the right one depends on your specific needs and priorities. In this guide, we’ll help you make an informed decision by outlining the key factors to consider when choosing between sponge iron and pig iron.
1. Application Requirements
The first and foremost consideration when deciding between sponge iron and pig iron is your application’s requirements. The type of iron you choose should align with the properties and characteristics needed for your end product or process.
Sponge Iron
- Low Carbon Content: Sponge iron has a low carbon content, typically less than 0.1%. This makes it suitable for applications where a clean, low-carbon iron is essential, such as steel production in electric arc furnaces (EAF) or induction furnaces.
- Minimal Impurities: Sponge iron is relatively pure, with minimal impurities like silicon, phosphorus, and sulfur. This purity is advantageous in processes where impurities can negatively affect the final product.
Is Sponge Iron Right for You?
Choose sponge iron if your application requires low-carbon, clean iron with minimal impurities. It is commonly used in steelmaking, iron casting, powder metallurgy, and the production of welding electrodes.
Pig Iron
- High Carbon Content: Pig iron has a high carbon content, typically around 3-4%. This high carbon content is beneficial for applications where the presence of carbon is desirable, such as in the production of cast iron and certain types of steel.
- Variable Impurities: Pig iron contains various impurities, including silicon, phosphorus, and sulfur, at varying levels. These impurities can influence the properties of the final product.
Is Pig Iron Right for You?
Opt for pig iron if your application requires high-carbon iron or if you’re involved in cast iron production, foundry work, or alloy production.
2. Environmental Considerations
In today’s world, environmental impact is a significant consideration for many industries. The choice between sponge iron and pig iron can have implications for your organization’s sustainability goals and environmental compliance.
Sponge Iron
- Lower Carbon Emissions: Sponge iron production generally results in lower carbon emissions compared to pig iron production. The direct reduction process used in sponge iron production is more energy-efficient and emits fewer greenhouse gases.
Consider Sponge Iron If:
- Your organization prioritizes reducing carbon emissions and strives to adopt greener technologies.
- You need to meet environmental regulations that impose restrictions on carbon emissions.
Pig Iron
- Higher Carbon Emissions: Pig iron production, especially through blast furnace smelting, is associated with higher carbon emissions due to the use of coke as a reducing agent.
Consider Pig Iron If:
- Your application requirements necessitate the use of pig iron, despite its higher carbon footprint.
- Environmental considerations are secondary to other factors like cost or application suitability.
3. Cost Analysis
Cost considerations play a significant role in choosing between sponge iron and pig iron. It’s essential to assess both the direct and indirect costs associated with each type of iron.
Sponge Iron
- Production Costs: Sponge iron production may involve higher capital costs for setting up direct reduction plants and equipment. However, operational costs, including energy consumption, are generally lower.
- Raw Material Costs: The cost of iron ore and reductants (such as natural gas or coal) significantly impacts the overall cost of sponge iron production.
Consider Sponge Iron If:
- You can justify the initial capital investment for long-term operational cost savings.
- The cost of iron ore and reductants is competitive in your region.
Pig Iron
- Production Costs: Pig iron production in blast furnaces often involves lower capital investment due to existing infrastructure but higher operational costs due to energy-intensive processes.
- Raw Material Costs: The cost of iron ore, coke, and limestone affects the cost of pig iron production.
Consider Pig Iron If:
- Your organization prioritizes lower initial capital expenditures over long-term operational costs.
- Existing infrastructure for blast furnace smelting is available and cost-effective.
4. Technological Advancements
The iron and steel industry is continuously evolving, with ongoing advancements in production technologies. Keeping up with these innovations can influence your decision between sponge iron and pig iron.
Sponge Iron
- Technology Advancements: Advances in direct reduction technologies may further improve the efficiency and environmental performance of sponge iron production.
Consider Sponge Iron If:
- You are open to adopting the latest technologies and incorporating them into your production processes.
- Sustainability and efficiency are essential aspects of your organization’s growth strategy.
Pig Iron
- Technology Advancements: Blast furnace technology has been refined over many years, and improvements continue to be made to increase energy efficiency and reduce emissions.
Consider Pig Iron If:
- You have existing blast furnace infrastructure and can benefit from ongoing advancements in this technology.
- Your application requires the unique properties of pig iron.
5. Future Sustainability Goals
Consider your organization’s long-term sustainability goals and how they align with the choice of iron type. Sustainability encompasses environmental impact, cost efficiency, and adaptability to changing market conditions.
Consider Sponge Iron If:
- You aim to reduce your organization’s carbon footprint and contribute to a more sustainable future.
- You are looking to align your operations with emerging environmental regulations and consumer preferences for eco-friendly products.
Consider Pig Iron If:
- Your organization’s sustainability goals prioritize other aspects, such as cost savings or product quality.
- The unique properties of pig iron are essential for your specific applications.
6. Conclusion
The choice between sponge iron and pig iron is not a one-size-fits-all decision. It hinges on your application’s requirements, environmental considerations, cost analysis, technological readiness, and long-term sustainability goals. Both types of iron have their merits and applications, and your decision should align with your organization’s priorities and objectives.
FAQs
Sponge Iron, also known as Direct-Reduced Iron (DRI), is produced by reducing iron ore using a reducing gas or solid reductant at lower temperatures, resulting in a porous, sponge-like structure.
Pig Iron is an intermediate product produced by smelting iron ore in a blast furnace. It contains a higher carbon content and impurities, making it unsuitable for most applications in its raw form.
Sponge Iron has low carbon content (typically less than 0.1%) and minimal impurities, whereas Pig Iron contains around 3-4% carbon and variable impurities like silicon, phosphorus, and sulfur.
Sponge Iron is used in steel production, iron casting, powder metallurgy, and welding electrodes. Pig Iron is primarily used in cast iron production, foundry work, and some types of steelmaking.
Sponge Iron production generally results in lower carbon emissions and is more energy-efficient compared to Pig Iron production, which is associated with higher carbon emissions and energy-intensive processes.
The cost-effectiveness depends on various factors, including raw material costs, production scale, and regional considerations. Sponge Iron may have lower operational costs but higher initial capital investment, while Pig Iron might have lower upfront costs but higher operational expenses.
Yes, Sponge Iron can be used in recycling processes due to its low impurity content, making it a viable choice for organizations emphasizing sustainability and circular economy principles.
Yes, both Sponge Iron and Pig Iron production processes continue to see advancements in technology aimed at improving efficiency, reducing environmental impact, and enhancing product quality.
Consider your application requirements, environmental goals, cost analysis, technological readiness, and long-term sustainability objectives when making the choice between Sponge Iron and Pig Iron.
You can explore comprehensive guides and articles, like the one provided here, or consult industry experts for in-depth insights tailored to your specific needs.
Read More:
Contents